- Регистрация
- 17.08.2019
- Сообщения
- 54
- Реакции
- 138
- Баллы
- 103
- Город
- Арзамас
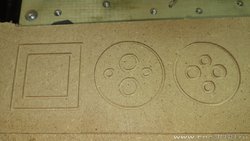
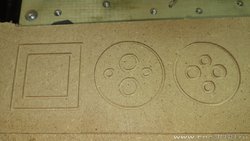
Вот такая красота появилась после работы на втулках
Follow along with the video below to see how to install our site as a web app on your home screen.
Примечание: This feature currently requires accessing the site using the built-in Safari browser.
Уже проходили.Все сюрпризы ждут когда станок уже собран, втулки поставлены, валы на своих местах и пыльца от кипящей работы не спешно осаживается на валы
Простите но прямо противоположное хочу сказать, во первых на втулке обязательно должна присутствовать фаска, чем меньше угол захода, тем сложнее втулки клин, во вторых, что за абразив у вас при резке плат? Там только медь и стеклопластик, оба материала имеют твердость ниже чем латунь, в связи с этим абразивом не может являться, вот теперь о смазке, я на 3д принтерах такие втулки смазываю раз в полгода, да и то не втулки а вал, на цпц один раз за месяца 4 ,тряпкой смоченной машинным маслом (синтетикой, хотя не важно, и ШРУС-4 смазывал) потом бумажной салфеткой вытирал вал, не нужно что бы с него масло текло, нужно получить слегка жирную поверхность (что бы любые "абразивы" не могли скоксоваться, а то что они попадут внутрь втулки, ничего страшного, как попадет , так и выйдет,) при большом кол-ва смазки графит начинает разрушаться, он имеет очень большую твердость при очень мелкой фракции, налипая на латунь он образует легко разрушаемую защитную поверхность, заливаясь во все щели , как таковая смазка для графита не нужна вовсе, но вот что бы графит к валу прилип, нужно что то , без разницы что, лишь бы увеличить прилипание, чем твёрже материал с которым предстоит работать, тем меньше смазки должно оставаться на валу.![]()
Вот такая красота появилась после работы на втулкахНеожиданно, но если начинать подробно изучать тему, то все получается весьма логично. Про графит - абразивом он не является, потому как имеет совсем обратные свойства, широко применяется в смазках, втулках... достаточно потереть графитовый порошок пальцами, для сомневающихся можно провести опыт - разберите дрель, болгарку, шуруповерт... и увидите графитовые щетки трущиеся годами о медный коллектор - мягкий и вязкий материал, при этом стираются щетки а коллектор имеет небольшой износ. Пыльники, сальники, манжеты , набивки - увы без этого ничего на втулках не будет работать адекватно на станках где идет резание, фрезеровка, сверловка. На моих стоковых подшипниках сальники работали на отлично ! Никакого скопления грязи я не обнаружил. Сейчас вижу как пыль пресуется втулками и ничего не мешает ей постепенно попадать во втулку. Смазка - жидкая, густая... главное что бы она была внутри подшипников и втулок а не на поверхности вала, активно прилепляя к себе пыль и абразив. В случае обработки текстолита - это именно абразив ! Не зря для работы с ним применяют твердосплавной инструмент. Посмотрим на то что изобретено пару сотен лет назад - токарные станки, где много втулок и пришабреных ласточкиных хвостов - везде имеются отверстия, канавки, каналы для подачи смазки. Для нормальной работы втулки смазка должна подаваться внутрь втулки, увы ) Я соблазнился на "самосмазывающиеся бронзо-графитовые втулки", в надежде работать без смазки... вроде замечательная пара трения - сталь, бронза\латунь и графит,увы не прокатило ! Капать маслом на направляющие - малоэффективно и высокоэффективно в плане испортить заготовку масляными пятнами. На сегодняшний момент - втулки стоят на оси X и Z, по оси Y не удалось победить заклинивания в процессе работы, поставил подшипники назад
) Прихожу к выводу, что нет смысла переходить на втулки - нет точности в изготовлении деталей станка, нет "мяса" для грамотной и работающей системы сальников\пыльников\манжет, нет системы смазки. Втулки ставим для повышения точности и уж потом для уменьшения шума от станка, получаем заметно тугое перемещение по осям, следственно интенсивный износ гаек ходовых винтов и получаем ухудшение точности работы станка. От чего ушли к тому и пришли !!! Адекватная замена выработавшихся подшипников, наверно лучшее средство для такого станка
![]()
СТЕКЛОтекстолит. Слово "СТЕКЛО" вам ни о чем не говорит? Мне приходилось обрабатывать стеклотекстолит на токарном, резца на 2 прохода не хватало. А фрезы Р6М5 вообще стирало напрочь. Обычный текстолит без проблем обрабатывается любым режущим инструментом, хоть быстрорез, хоть твердосплав, хоть напильник.что за абразив у вас при резке плат? Там только медь и стеклопластик
Алмаз вам ни о чем не говорит? А ведь графит ближайший родственник алмазу, или стекло твёрже алмаза? Но тогда почему графит используется в качестве смазки? Да и грифели карандашей рисуют же, дело не в стекле и его трердости, дело в том что стеклоткань состоит из макроскопических нитей стекла, иначе она просто потеряла бы гибкость, так вот микро стекло вообще никак не может стереть втулку, ибо микрочастицы графита твёрже любого стекла, смола по сравнению с графитом вообще можно сказать что "пластилин" твердость минимальная, поэтому и втулке эта пыль особо не страшна, хуже обстоит дело с деревом, смолы (жидкие) которые есть в дереве, могут налипать на втулку и вал, графит ,налипая на эту субстанцию, коксуется, создавая трудно разрушаемый слой, втулка забивается , а графит продолжает налипать, в конечном итоге ход втулки становится тяжелее и так до подклинивания и полной остановки.. и не путайте, обработку (когда фреза пытается отколоть микро кусок ,часто попадая в микро волокна стекла тор, и движение по этой самой суьСТЕКЛОтекстолит. Слово "СТЕКЛО" вам ни о чем не говорит? Мне приходилось обрабатывать стеклотекстолит на токарном, резца на 2 прохода не хватало. А фрезы Р6М5 вообще стирало напрочь. Обычный текстолит без проблем обрабатывается любым режущим инструментом, хоть быстрорез, хоть твердосплав, хоть напильник.
Но тогда почему графит используется в качестве смазки?
Парадокс. На такие доводы и ответить нечего. Пойду учебник почитаю, а то все форумы да чаты. Прям идиотом себя чувствую.ибо микрочастицы графита твёрже любого стекла
Алмаз - одна из аллотропных модификаций углерода и самое твердое из известных веществ. Другая аллотропная модификация углерода – графит – одно из самых мягких веществмикрочастицы графита твёрже любого стекла,
Алмаз, спеченный под давлением графит, я видел как технические алмазы выращивают, давно правда это было, ещё при совке, как материал чешуйка графита имеет плотность около 2,5 г/мм квадратный плюс минус, у волокна стекла примерно 2,1г/мм квадратный , у алмаза 3,4 (если мне память не изменяет) , сам по себе графит как материал мягкий, но его частицы очень твердые, кстати антифрикционные свойства алмаза прикольные, если сделать втулку с алмазным покрытием на наш станок, то ее смазывать вообще не нужно, вал очень быстро выгладится но последующий износ будет самым минимальным из возможных.Алмаз - одна из аллотропных модификаций углерода и самое твердое из известных веществ. Другая аллотропная модификация углерода – графит – одно из самых мягких веществ
Отсюда взял.
А мне казалось, что прочность зависит от формы кристаллической решетки, а не от плотности. у свинца плотность 11,37 и он не является образивомАлмаз, спеченный под давлением графит, я видел как технические алмазы выращивают, давно правда это было, ещё при совке, как материал чешуйка графита имеет плотность около 2,5 г/мм квадратный плюс минус, у волокна стекла примерно 2,1г/мм квадратный , у алмаза 3,4 (если мне память не изменяет) , сам по себе графит как материал мягкий, но его частицы очень твердые, кстати антифрикционные свойства алмаза прикольные, если сделать втулку с алмазным покрытием на наш станок, то ее смазывать вообще не нужно, вал очень быстро выгладится но последующий износ будет самым минимальным из возможных.
Вам тоже хотел сказать, что углерод он хоть и в Африке углерод, но это элемент с самым большим количеством аллотропных модификаций!углерод он и в африке углерод. другое дело структура. граффит как чешуйки структурой поэтому он легко расслаиваетсяи мягкий.. алмаз структурой пирамидальный как бы кристал поэтому крепкий.и то и это хорошо горит так как элемент один и тот же нокрепкость абсолютно разная.
Нее, лучше вот эти. И в стальном крпусе с проточкой под фиксирующие кольца, и с пыльниками. Но на Али я их найти не смог
Интернет портал организованный в 2018 году , для поддержки пользователей мини станка с ЧПУ CNC 3018 и его модификаций.
Мы хотели бы помочь всем, кто приобрел или только собирается приобрести данный станок. Здесь Вы совершенно спокойно можете задать свои вопросы, или просто прочитать полезную или интересную информацию по сборке, настройке и эксплуатации данного мини станка.
МЫ ДОГАДЫВАЕМСЯ, ЧТО РЕКЛАМА ВАС РАЗДРАЖАЕТ!
Конечно, Ваше программное обеспечение для блокировки рекламы отлично справляется с блокировкой рекламы на нашем сайте, но оно также блокирует полезные функции. Мы стараемся для Вас и не обязываем Вас донатить и скидывать денег на наши кошельки, чтобы пользоваться форумом, но реклама это единственное, что позволяет поддерживать проект и развивать его.
Спасибо за Ваше понимание!