- Регистрация
- 28.09.2020
- Сообщения
- 79
- Реакции
- 117
- Баллы
- 335
- Адрес
- Казахстан
- Город
- Астана
- Имя
- Виктор
- Отчество
- Васильевич
- Станок
- CNC2030
- Плата
- ver 3.0, Bachin
- Прошивка
- 1.1f
Последнее редактирование:
Во второй половине января пришёл ко мне мой новый станочек CNC2030. Поделюсь с вами своими впечатлениями и доработками....
Итак, пожалуй, начну с особенностей конструкции.
Основанием для оси Y является пластина металла толщиной 3,4 мм размером 260х425 мм изогнутая в виде буквы «П». К ней прикручены два цилиндрических рельса 12 мм диаметром. Расстояние между рельсами 130 мм по центрам.
Вертикальные стойки, высотой 340 мм, изготовлены из прямоугольной металлической трубы, размером 40х80 мм, толщина стенки трубы 1,6 мм.
Опорная плита оси X выполнена из листового металла толщиной 2,8 мм, размером 115х300 мм согнутого в виде буквы «П». Цилиндрические рельсы диаметром 12 мм имеют длину 300 мм и расстояние 70 мм по центрам.
Опорная плита оси Z выполнена из металла толщиной 2,4 мм размером 115х185 мм изогнутого в виде буквы «П». Цилиндрические рельсы также диаметром 12 мм имеют длину 185 мм и расстояние 70 мм по центрам. Пластина для крепления шпинделя имеет размеры 115х90 и толщину 5 мм. Стандартный держатель для шпинделей диаметром 52 мм удерживает электродвигатель 400 Вт, 48В. Электродвигатель имеет патрон ER11.
Вся конструкция собрана на болтах с резьбой М5 и М6. Что характерно, нет ни одной гайки, резьбы нарезаны в металле опорных плит. Единственно в местах крепления вертикальных стоек к пластине оси Y приварены небольшие L-образные усилители в которых нарезана резьба М6. Вертикальные стойки крепятся четырьмя болтами М6 к опорной пластине оси Y.
Опорная плита оси X крепится к вертикальным стойкам болтами М6, резьба для которых нарезана в стенке трубы толщиной 1,6 мм. На такой толщине нет даже двух ниток резьбы, но, тем не менее, все болты закручены крепко и ничего не болтается.
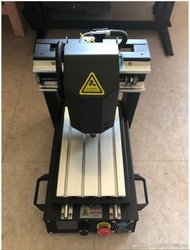
Отсек управления расположен под опорной плитой оси Y и содержит в себе плату управления, от компании Bachin с прошивкой 1.1z, блок питания 12В для платы управления и блок питания 48В для шпинделя. На лицевой стороне отсека управления находится дисплей off-line контроллера. В режиме работы от off-line контроллера, управление станком производится энкодером, расположенным рядом с дисплеем. Охлаждение отсека управления производится вентилятором, расположенным на передней панели. С правой стороны отсека управления находится гнездо для подключения карты памяти формата SD, очень удобная фишка для поддержания автономной работы станка. Далее находится гнездо для подключения зонда оси Z. Имеются также два выключателя – один для принудительного включения шпинделя, второй для общего вкл/выкл станка. Здесь же находится гнездо для подключения компьютера по USB шнуру. Станок по USB управляется программой Candle версии 1.1.8. На задней стенке находится гнездо С14, для подключения сети 220В. Стандартный шнур с EVRO-вилкой и разъемом С13 идет в комплекте со станком.
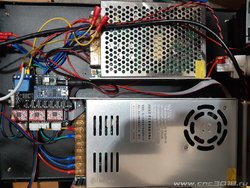
Все оси приводятся в движение ходовыми винтами TR8x2x8. Винты с обоих концов закреплены в опорных подшипниках. Крутящий момент от шаговых двигателей (NEMA17) к ходовым винтам передается ременной передачей. Коэффициент передачи 3:1. Ходовой винт оси Y сверху по всей длине закрыт декоративным щитком. Шпиндель так же прикрыт декоративным колпаком, который помимо функции безопасности ещё является направляющим элементом, для правильной организации воздушного потока охлаждения электродвигателя.
Рабочий стол из алюминиевого профиля 295х180 мм имеет толщину 15 мм и крепится четырьмя болтами М6, с закладными гайками, к опорной плите оси Y.
Про описание конструкции, в общем, то всё.
Ну а далее наступили суровые будни.
Сначала станок был дополнен жертвенным столиком из двух кусков ЛДСП общей толщиной 32 мм. В верхнюю часть жертвенного столика были вставлены 24 штуки, так называемых «гайка-шип», с резьбой М6 для пластиковых креплений ПП. Верхняя часть прикручена шурупами, впотай, к нижней.
При фрезеровке поверхности жертвенного стола выявился первый «косяк». Левая сторона оказалась завалена на примерно 1 мм. Переборка крепежа вертикальных стоек оси X ничего не дала. Всё осталось по-прежнему. Отверстия под крепёж просверлены очень точно, а доработать напильником не захотелось.
Не знаю, чем это будет грозить в будущем, но фреза в плоскостях XY стоит вертикально под 90[SUP]0[/SUP] по отношению к жертвенному столу.
Так как станок не был оборудован конечными выключателями, я решил их установить. Ещё 2019 году я заказывал для своего CNC2020 комплект из 6-ти выключателей. Но поставил только три. Вот и оставшиеся три пригодились.
Это по оси Y
Это по оси X
Ну и по Z соответственно.
После установки конечных выключателей решил проверить работу функции «Дом» и к своей досаде обнаружил, что ось Z в этом не участвует. Т.е. оси X и Y движутся, а ось Z нет. Косяк оказался в прошивке. Прошивка 1.1z, установленная на станке, «заточена» под лазеры, а её воткнули во фрезерный станок. Вот спрашивается – где логика?
Пришлось заменить прошивку на 1.1f. Всё вроде встало на свои места. Решил, что всё, мои трудности позади.
Ага, щазззз (размечтался!)… Первый же опыт фрезеровки ПП меня просто обескуражил.
Такого позора у меня не было даже на моём пластиковом CNC2020, а здесь полностью металлический станок. Контактные площадки непонятной формы, дорожки погрызены, отверстия не в центре площадок – короче полный отстой.
Итак, пожалуй, начну с особенностей конструкции.
Основанием для оси Y является пластина металла толщиной 3,4 мм размером 260х425 мм изогнутая в виде буквы «П». К ней прикручены два цилиндрических рельса 12 мм диаметром. Расстояние между рельсами 130 мм по центрам.
Вертикальные стойки, высотой 340 мм, изготовлены из прямоугольной металлической трубы, размером 40х80 мм, толщина стенки трубы 1,6 мм.
Опорная плита оси X выполнена из листового металла толщиной 2,8 мм, размером 115х300 мм согнутого в виде буквы «П». Цилиндрические рельсы диаметром 12 мм имеют длину 300 мм и расстояние 70 мм по центрам.
Опорная плита оси Z выполнена из металла толщиной 2,4 мм размером 115х185 мм изогнутого в виде буквы «П». Цилиндрические рельсы также диаметром 12 мм имеют длину 185 мм и расстояние 70 мм по центрам. Пластина для крепления шпинделя имеет размеры 115х90 и толщину 5 мм. Стандартный держатель для шпинделей диаметром 52 мм удерживает электродвигатель 400 Вт, 48В. Электродвигатель имеет патрон ER11.
Вся конструкция собрана на болтах с резьбой М5 и М6. Что характерно, нет ни одной гайки, резьбы нарезаны в металле опорных плит. Единственно в местах крепления вертикальных стоек к пластине оси Y приварены небольшие L-образные усилители в которых нарезана резьба М6. Вертикальные стойки крепятся четырьмя болтами М6 к опорной пластине оси Y.
Опорная плита оси X крепится к вертикальным стойкам болтами М6, резьба для которых нарезана в стенке трубы толщиной 1,6 мм. На такой толщине нет даже двух ниток резьбы, но, тем не менее, все болты закручены крепко и ничего не болтается.
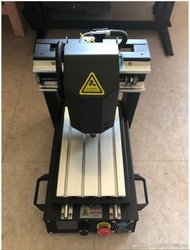
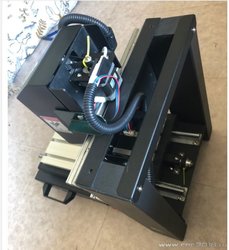
Отсек управления расположен под опорной плитой оси Y и содержит в себе плату управления, от компании Bachin с прошивкой 1.1z, блок питания 12В для платы управления и блок питания 48В для шпинделя. На лицевой стороне отсека управления находится дисплей off-line контроллера. В режиме работы от off-line контроллера, управление станком производится энкодером, расположенным рядом с дисплеем. Охлаждение отсека управления производится вентилятором, расположенным на передней панели. С правой стороны отсека управления находится гнездо для подключения карты памяти формата SD, очень удобная фишка для поддержания автономной работы станка. Далее находится гнездо для подключения зонда оси Z. Имеются также два выключателя – один для принудительного включения шпинделя, второй для общего вкл/выкл станка. Здесь же находится гнездо для подключения компьютера по USB шнуру. Станок по USB управляется программой Candle версии 1.1.8. На задней стенке находится гнездо С14, для подключения сети 220В. Стандартный шнур с EVRO-вилкой и разъемом С13 идет в комплекте со станком.
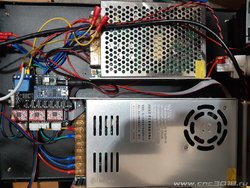
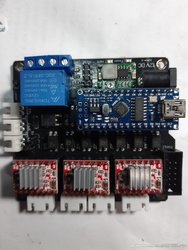
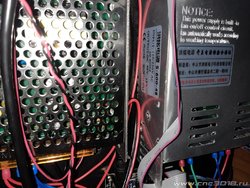
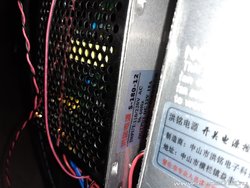
Все оси приводятся в движение ходовыми винтами TR8x2x8. Винты с обоих концов закреплены в опорных подшипниках. Крутящий момент от шаговых двигателей (NEMA17) к ходовым винтам передается ременной передачей. Коэффициент передачи 3:1. Ходовой винт оси Y сверху по всей длине закрыт декоративным щитком. Шпиндель так же прикрыт декоративным колпаком, который помимо функции безопасности ещё является направляющим элементом, для правильной организации воздушного потока охлаждения электродвигателя.
Рабочий стол из алюминиевого профиля 295х180 мм имеет толщину 15 мм и крепится четырьмя болтами М6, с закладными гайками, к опорной плите оси Y.
Про описание конструкции, в общем, то всё.
Ваши сообщения автоматически объединены:
Ну а далее наступили суровые будни.
Сначала станок был дополнен жертвенным столиком из двух кусков ЛДСП общей толщиной 32 мм. В верхнюю часть жертвенного столика были вставлены 24 штуки, так называемых «гайка-шип», с резьбой М6 для пластиковых креплений ПП. Верхняя часть прикручена шурупами, впотай, к нижней.
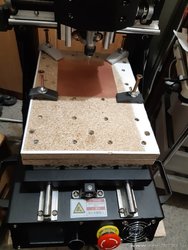
При фрезеровке поверхности жертвенного стола выявился первый «косяк». Левая сторона оказалась завалена на примерно 1 мм. Переборка крепежа вертикальных стоек оси X ничего не дала. Всё осталось по-прежнему. Отверстия под крепёж просверлены очень точно, а доработать напильником не захотелось.
Не знаю, чем это будет грозить в будущем, но фреза в плоскостях XY стоит вертикально под 90[SUP]0[/SUP] по отношению к жертвенному столу.
Так как станок не был оборудован конечными выключателями, я решил их установить. Ещё 2019 году я заказывал для своего CNC2020 комплект из 6-ти выключателей. Но поставил только три. Вот и оставшиеся три пригодились.
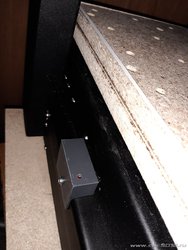
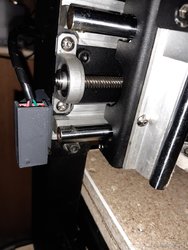
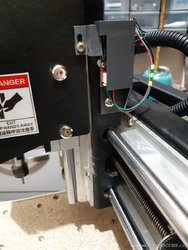
После установки конечных выключателей решил проверить работу функции «Дом» и к своей досаде обнаружил, что ось Z в этом не участвует. Т.е. оси X и Y движутся, а ось Z нет. Косяк оказался в прошивке. Прошивка 1.1z, установленная на станке, «заточена» под лазеры, а её воткнули во фрезерный станок. Вот спрашивается – где логика?
Пришлось заменить прошивку на 1.1f. Всё вроде встало на свои места. Решил, что всё, мои трудности позади.
Ага, щазззз (размечтался!)… Первый же опыт фрезеровки ПП меня просто обескуражил.
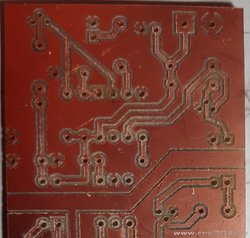
Такого позора у меня не было даже на моём пластиковом CNC2020, а здесь полностью металлический станок. Контактные площадки непонятной формы, дорожки погрызены, отверстия не в центре площадок – короче полный отстой.