- Регистрация
- 13.06.2020
- Сообщения
- 8
- Реакции
- 14
- Баллы
- 73
- Город
- Новосибирск
- Имя
- Дмитрий
- Станок
- CNC 3018 Max
- Плата
- Woodpecker 3.1
Вся эта статья задумывается как просьба о помощи к людям, которые давно ковыряются в теме CNC3018, да и просто теме фрезерования. Просьба следующего характера: посмотреть на то, что я тут наворотил и показать на места, которые даже не стоит пробовать делать. Пока еще не поздно, пока все только в памяти моего компьютера. Ведь переделывать что-то значительное, после того как все собрал и понял, что тут не работает довольно тяжело. Приступим.
Началось всё давно... В мае 2020 года во времена ковида, полной изоляции, удаленной учебы и т.д. Тогда был приобретён станок CNC 3018 PRO MAX, full metal который. И, судя по покупкам на «Али», уже в июне у меня зачесались руки.
После нескольких попыток фрезеровки дерева, оргстекла и печатных плат понял, что ему не хватает жёсткости. И проблема крылась в направляющих: цилиндрическая направляющая диаметром 12 мм заметно прогибалась от легкого прикосновения к фрезе, если каретка стояла посередине оси.
Ещё одной проблемой был огромный люфт гаек ходовых винтов. Из-за этого относительно точные изделия (печатные платы) получались сомнительные.
Третья - отвратительная ось Z. Даже комментировать не хочу.
Поняв эти моменты, решил доработать станок. Вопрос - как? Тогда я еще был студентом, деньги экономить нужно было как можно больше. От второй проблемы избавился с помощью холодной сварки. Просто замазав посадочное место подвижной гайки на всех трех осях. Видимый люфт на гайках исчез, но обнаружился люфт на подшипниках KFL08. Гораздо меньше, чем на гайках, но он есть, и его видно. Вычитал на форумах, что это из-за подшипников и что можно попробовать купить другие. Попробовал - помогло. Видимый люфт ушёл.
А теперь первая проблема. Понятно, что решить ее можно только заменой направляющих. Какие ставить? Цилиндрические, но большего диаметра ставить смысл, наверное, есть. Но в ущерб рабочему пространству и с ограничением по габаритам (чтобы подшипник направляющей не упирался в стенку).
Цилиндрические с ребром жесткости (SBR) не хотелось ставить из-за разрезанного линейного подшипника. Уж очень он не внушает доверия, хотя жёсткости там на прилично больше. На этот вариант смотрел меньше всего.
Ну и последний - профильные направляющие. Очень уж вкусным выглядел вариант купить Hiwin, но студенческая жизнь мне этого не позволяла. Оставались китайские аналоги, и, судя по отзывам, довольно неплохие. Цена высоковата, но за несколько заходов купить можно. Что ж, решил – профильная китайская направляющая.
От третьей проблемы просто избавился. Использовать родную каретку X не видел никакой возможности.
Начал с оси Z. Направляющие MGN12, L=150 мм (пришли 149, но это даже к лучшему) + алюминиевый усиленный профиль 20х20 соответствующей длины + набор крепежа и вперед моделировать. Тогда 3D-печать еще не была распространена в тех кругах, в которых я общался. Но был относительно неплохой фрезерный ЧПУ станок. Поэтому первый вариант моделировался с учетом того, что он будет фрезероваться (забегаю вперед, этого не случилось). Тут же столкнулся с тем, что длины родного трапециевидного ходового винта не хватает, а купить новый чуть длиннее не выйдет, так как винт является частью шагового двигателя. Что ж, покупаем китайскую ШВП SFU1204, L=200 мм и шаговый двигатель Nema 17.
Оси X и Y. Изначально в планах была направляющая MGN15 на обе оси. Но в один момент наткнулся на «Авито» на продажу поддержанных комплектующих для станков с ЧПУ, где и приобрёл 2 направляющие THK23, L=279 мм и одну INA20, L=400 мм за какие-то смешные 2500 рублей за все. Направляющие шикарные. Ходят с натягом, но небольшим. Одна немного подзаедает на конце, но это не страшно. Направляющие THK23 отправил на ось Y. Длины немного не хватает, но через проставки выставил их на центр. Там, где рельсы нет, подшипник все равно ходить не будет из-за габаритов стола. Направляющую INA20 разместил на ось X. Понятно, что одной рельсы будет мало, поэтому в довесок к ней докупил китайскую MGN15, L=360 мм.
Направляющие THK23 на штатные места цилиндрических направляющих не установить. Купил 5 усиленных профилей 20х20, L=360 мм у «Соберизавода» (не реклама, но профиль у них хороший, режут в размер, торцы ровные (по крайней мере, были 3 года назад
. Но крепеж у них дорогой. Уголки, сухари и винты купил комплектом на «Али». На оси X штатный профиль 20х40 заменил на 20х60 от тех же ребят. Так направляющая INA20 легла на стойки станка, не встала между ними.
На этом работа по допиливанию станка надолго встала. Учеба, работа, диплом, переезд, снова работа и наконец отпуск, когда у меня не получилось никуда вырваться. К этому времени я приобрел уже два 3D-принтера и не могу не учитывать этот момент при проектировании.
Снова моделировать… Не знаю, сколько часов ушло всего, но очень много.
Следующей проблемой, которая надолго меня остановила, заключалась в люфтах на ходовых винтах. Для упрощения своей жизни принял китайскую ШВП на оси Z
за безлюфтовую, но понимаю, что это не так. Холодную сварку, которая показала себя более-менее достойно, использовать как постоянный вариант желания не было. Да и не понятно, как она поведет себя при постоянных нагрузках. Вариант с расклиниваем двух гаек, как это делается на полноценных станках, меня не совсем устраивал из-за его габаритов. Не получилось уместить 2 гайки, жесткий клин и несколько винтов в таком ограниченном пространстве. Вариант с разжиманием/сжиманием двух ходовых гаек с помощью винтов мне показался сомнительным из-за перекоса одной из гаек при затяжке винтов. Поэтому реализовал тот же вариант, что был изначально, но немного его усовершенствовал: 1) Поставил чуть более мощную пружину взамен штатной; 2) Подвижная гайка после разжимания пружины теперь фиксируется на 4 винта, что обеспечивает ее неподвижность. Наверное, такой вариант тоже не обеспечивает отсутствие перекоса... Если кто желает поделиться опытом по этому поводу, буду рад почитать.
Когда с люфтом на гайках разобрался, осталось по мелочи. Раскидать крепеж, поставить концевики (приобрел еще в первый заход модернизации индуктивный, а теперь не знаю, можно их поставить на дятла или нет) и продумать кабель-менеджмент. Первые два пункта готовы. Последний буду думать непосредственно при сборке станка.
Пробежался по тому, как что делалось. Теперь попробую подробно описать что из этого вышло.
Начнем с каретки Z и шпинделя
Шпиндель на 300 Вт, родной. Кронштейн был приобретен на «Али» вместе с винтами, но последние оказались коротковаты и были заменены. Кронштейн шпинделя крепится через соединительную проставку к линейным подшипникам и ходовой гайки ШВП. Проставка планируется печататься из PETG или композитов в угоду большей жесткости. Винты кронштейна закручиваются во вкладываемые гайки. Для компактности кронштейн ходовой гайки придется немного подпилить.
Каретка оси X
Она была наиболее сложной в том плане, чтобы ничего не упустить. Линейные подшипники, ходовые гайки (которые еще и распереть надо), рельсы оси Z, ШВП оси Z (которую так же нужно закрепить, да еще и без люфтов), ШД, муфта, крепеж, не забыть шайбу под каждый винт… В общем, намучался. Этот вариант будет печататься из композита (посматриваю на PP GF30). Потом, скорее всего, фрезеровка каретки на этом же станке.
Сама каретка представляет собой П-образную конструкцию, со множеством отверстий и выемок. Ничего сложного. Но есть два проблемных места: 1- ходовой винт оси Z; 2 – ходовая гайка оси X. Пойдем по порядку.
Уберем все лишнее, разрежем и посмотрим на винт ШВП.
Сверху на винт накручивается гайка низкая М10 (резьбу необходимо нарезать до нужной длины). После этого, винт продевается в два отверстия. Снизу ложится на упорный игольчатый подшипник AXK0821. Сверху через подшипник AXK1024 поджимается гайкой к верхней стенке, тем самым распирается и жестко встает на свое место. После этого накидывается второй подшипник AXK1024 и поджимается второй низкой гайкой М10 (на изображении ее нет, случайно убрал). Гайки садятся на фиксатор резьбы. Так винт без люфтов (очень на это надеюсь) встанет на свое место
Механизм распорки гаек ходового винта оси X. Обе латунные гайки крепятся через 4 винта М3 к напечатанным деталям. Закручиваться будут в гайки, которые закладываются в деталь на этапе печати (напечатал до нужной высоты, поставил паузу, заложил нужную деталь, продолжил печать), благо что слайсеры позволяют ставить паузы на нужном слое. Левая на картинке гайка подвижная. На каретке фиксируется четырьмя винтами М3 после распорки двух гаек пружиной.
Линейные направляющие MGN12 крепятся к алюминиевому профилю 20х20. Профиль к каретке крепится на пять винтов М3. Пять потому что шестой закрутить не имеется возможности из-за линейного подшипника оси X. С торцов к профилю винтами М6 притянутся верх и низ каретки. Это уменьшит прогиб стенок от распорки ходового винта. Плюс, верхние винты закрепят на каретке кронштейн шагового двигателя оси Z.
Сам кронштейн, помимо своей основной задачи, имеет отросток для установки концевика оси Z и технологическое окно для затягивания винтов на муфте. В целом, по оси X все.
Ось Y (она же стол)
Чего-то интересного тут нет. Решение с распором гайки ходового винта тут точно такое же, как и на оси X. Высота подшипников маловата, относительно того, что было на валах, по тому ставлю небольшую проставку (естественно - печатается). Также есть небольшой кронштейн с металлической пластиной для срабатывания индуктивного датчика.
Ну и напоследок. Рама
Каких-то серьезных изменений рама не потерпела. Только лишь усилилась и приобрела места под новые рельсы. Рассмотрим подробнее и начнем с основания.
На основание добавилось пять алюминиевых профилей 20х20, которые крепятся через уголки к профилю 40х40. Основной их задачей является удержание линейных направляющих оси Y. Помимо этого, они не плохо так добавили жесткости всей базе станка. Еще одно заметное изменение – это цилиндрические направляющие диаметром 12 мм, которые остались от оригинальной комплектации. Но теперь они играют роль стяжек (или распорок), между передней и задней стенками основания и увеличивают жесткость. Для их установки потребуется просверлить 2 отверстия диаметром 6.5 мм. Для этого будет проектироваться кондуктор. Возможно, имеет смысл добавить кронштейн для каждого профиля 20х20, чтобы дополнительно фиксировать бывшую направляющую, но пока без этого.
Ходовой винт теперь крепится подшипниками KFL08 с обеих сторон и не должен передавать продольную нагрузку на ШД. Для установки дополнительного подшипника в задней стенке рамы необходимо просверлить два отверстия. Кронштейн шагового двигателя оси Y крепится к раме четырьмя винтами М3, которые закручиваются непосредственно в ШД. На нем также имеется технологическое окно. Тут же на раме стоит концевик оси Y. Крутилки на оси решил оставить, может пригодится. Тем более что они есть в наличии. Резиновые ножки встали на свои новые места.
Из-за установки дополнительного подшипника увеличилась необходимая длина ходового винта. Таким образом, винт от оси X немного обрежется и перейдет на ось Y. А на ось X необходимо купить новый винт.
С базой все. Перейдем к порталу
Из крупных изменений тут только профиль 20х60 и линейные направляющие. Так же как и на ось Y, добавлен второй подшипник KFL08, под который требуется просверлить 2 отверстия на правой боковой стойке. Кронштейн ШД оси X крепится через отверстия, которые раньше нужны были для крепления цилиндрических направляющих, через винты М6 с плоской головкой. Это нужно для увеличения рабочего пространства станка. Концевик сидит на профиле 20х60.
Вроде, обо всем рассказал. Сейчас идет этап печати деталей в пустотелом варианте для проверки их геометрии (на текущий момент уже были выявлены недочеты). Потом станок будет собираться в пустотелом варианте, для проверки кинематики. И только после этого печатать полноценные детали и собирать в полноценный станок. Если можно так выразиться.
Пока что у меня есть надежды, что после доработок станок сможет тягаться с металлами. Хотя бы с цветными. Понятно, что не на заказ на нем работать, а исключительно для себя. Собственно, для этого все и затевалось. Но смущает место крепления портала к базе.
Ну и для удобства обсуждения выкладываю все, что сделал в формате STEP. Надеюсь, мои труды кому-нибудь пригодятся.
Планы на будущее:
1. Заменить все ходовые винты на ШВП. Если будет необходимость, рассмотрю варианты подороже для минимизации люфтов.
1.1. Сделать фрезерованную каретку оси X. Думаю, это входит в планы про ШВП.
1.2. Если фрезерованная каретка осуществится, то постараюсь сделать базовую каретку, а на нее вешай что хочешь. Хочешь – фрезер, хочешь – лазер.
3. Поставить более мощный шпиндель. И пооборотистее. На «Али» видал моторы с 20к оборотами, но очень сомневаюсь в этом. Вопрос пока не изучал.
4. Плата управления. На первое время хватит того, что есть. Но мне нужна четвертая ось.
5. Четвертая ось. Пока не уверен, но что-то мне подсказывает что она закроет часть моих хотелок в плане токарной обработки.
P.S. Заранее огромное спасибо каждому за прочтение всего того, что тут написано и добрый совет. В условиях ограниченного количества свободного времени не хотелось бы чтобы проект затих. Нужно довести его до конца, но есть сомнения в моей компетентности относительно некоторых вопросов. Основная проблема – отсутствие реального опыта фрезерования.
P.P.S. Если проект в целом будет интересен, рассмотрю вариант переделки модели под то, что планировалось изначально. То есть линейные направляющие MGN15.
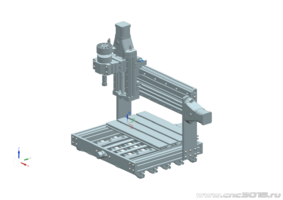
Началось всё давно... В мае 2020 года во времена ковида, полной изоляции, удаленной учебы и т.д. Тогда был приобретён станок CNC 3018 PRO MAX, full metal который. И, судя по покупкам на «Али», уже в июне у меня зачесались руки.
После нескольких попыток фрезеровки дерева, оргстекла и печатных плат понял, что ему не хватает жёсткости. И проблема крылась в направляющих: цилиндрическая направляющая диаметром 12 мм заметно прогибалась от легкого прикосновения к фрезе, если каретка стояла посередине оси.
Ещё одной проблемой был огромный люфт гаек ходовых винтов. Из-за этого относительно точные изделия (печатные платы) получались сомнительные.
Третья - отвратительная ось Z. Даже комментировать не хочу.
Поняв эти моменты, решил доработать станок. Вопрос - как? Тогда я еще был студентом, деньги экономить нужно было как можно больше. От второй проблемы избавился с помощью холодной сварки. Просто замазав посадочное место подвижной гайки на всех трех осях. Видимый люфт на гайках исчез, но обнаружился люфт на подшипниках KFL08. Гораздо меньше, чем на гайках, но он есть, и его видно. Вычитал на форумах, что это из-за подшипников и что можно попробовать купить другие. Попробовал - помогло. Видимый люфт ушёл.
А теперь первая проблема. Понятно, что решить ее можно только заменой направляющих. Какие ставить? Цилиндрические, но большего диаметра ставить смысл, наверное, есть. Но в ущерб рабочему пространству и с ограничением по габаритам (чтобы подшипник направляющей не упирался в стенку).
Цилиндрические с ребром жесткости (SBR) не хотелось ставить из-за разрезанного линейного подшипника. Уж очень он не внушает доверия, хотя жёсткости там на прилично больше. На этот вариант смотрел меньше всего.
Ну и последний - профильные направляющие. Очень уж вкусным выглядел вариант купить Hiwin, но студенческая жизнь мне этого не позволяла. Оставались китайские аналоги, и, судя по отзывам, довольно неплохие. Цена высоковата, но за несколько заходов купить можно. Что ж, решил – профильная китайская направляющая.
От третьей проблемы просто избавился. Использовать родную каретку X не видел никакой возможности.
Начал с оси Z. Направляющие MGN12, L=150 мм (пришли 149, но это даже к лучшему) + алюминиевый усиленный профиль 20х20 соответствующей длины + набор крепежа и вперед моделировать. Тогда 3D-печать еще не была распространена в тех кругах, в которых я общался. Но был относительно неплохой фрезерный ЧПУ станок. Поэтому первый вариант моделировался с учетом того, что он будет фрезероваться (забегаю вперед, этого не случилось). Тут же столкнулся с тем, что длины родного трапециевидного ходового винта не хватает, а купить новый чуть длиннее не выйдет, так как винт является частью шагового двигателя. Что ж, покупаем китайскую ШВП SFU1204, L=200 мм и шаговый двигатель Nema 17.
Оси X и Y. Изначально в планах была направляющая MGN15 на обе оси. Но в один момент наткнулся на «Авито» на продажу поддержанных комплектующих для станков с ЧПУ, где и приобрёл 2 направляющие THK23, L=279 мм и одну INA20, L=400 мм за какие-то смешные 2500 рублей за все. Направляющие шикарные. Ходят с натягом, но небольшим. Одна немного подзаедает на конце, но это не страшно. Направляющие THK23 отправил на ось Y. Длины немного не хватает, но через проставки выставил их на центр. Там, где рельсы нет, подшипник все равно ходить не будет из-за габаритов стола. Направляющую INA20 разместил на ось X. Понятно, что одной рельсы будет мало, поэтому в довесок к ней докупил китайскую MGN15, L=360 мм.
Направляющие THK23 на штатные места цилиндрических направляющих не установить. Купил 5 усиленных профилей 20х20, L=360 мм у «Соберизавода» (не реклама, но профиль у них хороший, режут в размер, торцы ровные (по крайней мере, были 3 года назад
На этом работа по допиливанию станка надолго встала. Учеба, работа, диплом, переезд, снова работа и наконец отпуск, когда у меня не получилось никуда вырваться. К этому времени я приобрел уже два 3D-принтера и не могу не учитывать этот момент при проектировании.
Снова моделировать… Не знаю, сколько часов ушло всего, но очень много.
Следующей проблемой, которая надолго меня остановила, заключалась в люфтах на ходовых винтах. Для упрощения своей жизни принял китайскую ШВП на оси Z
за безлюфтовую, но понимаю, что это не так. Холодную сварку, которая показала себя более-менее достойно, использовать как постоянный вариант желания не было. Да и не понятно, как она поведет себя при постоянных нагрузках. Вариант с расклиниваем двух гаек, как это делается на полноценных станках, меня не совсем устраивал из-за его габаритов. Не получилось уместить 2 гайки, жесткий клин и несколько винтов в таком ограниченном пространстве. Вариант с разжиманием/сжиманием двух ходовых гаек с помощью винтов мне показался сомнительным из-за перекоса одной из гаек при затяжке винтов. Поэтому реализовал тот же вариант, что был изначально, но немного его усовершенствовал: 1) Поставил чуть более мощную пружину взамен штатной; 2) Подвижная гайка после разжимания пружины теперь фиксируется на 4 винта, что обеспечивает ее неподвижность. Наверное, такой вариант тоже не обеспечивает отсутствие перекоса... Если кто желает поделиться опытом по этому поводу, буду рад почитать.
Когда с люфтом на гайках разобрался, осталось по мелочи. Раскидать крепеж, поставить концевики (приобрел еще в первый заход модернизации индуктивный, а теперь не знаю, можно их поставить на дятла или нет) и продумать кабель-менеджмент. Первые два пункта готовы. Последний буду думать непосредственно при сборке станка.
Пробежался по тому, как что делалось. Теперь попробую подробно описать что из этого вышло.
Начнем с каретки Z и шпинделя
Шпиндель на 300 Вт, родной. Кронштейн был приобретен на «Али» вместе с винтами, но последние оказались коротковаты и были заменены. Кронштейн шпинделя крепится через соединительную проставку к линейным подшипникам и ходовой гайки ШВП. Проставка планируется печататься из PETG или композитов в угоду большей жесткости. Винты кронштейна закручиваются во вкладываемые гайки. Для компактности кронштейн ходовой гайки придется немного подпилить.
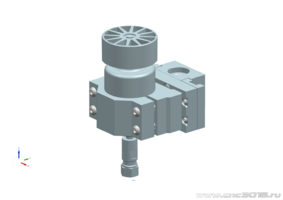
Каретка оси X
Она была наиболее сложной в том плане, чтобы ничего не упустить. Линейные подшипники, ходовые гайки (которые еще и распереть надо), рельсы оси Z, ШВП оси Z (которую так же нужно закрепить, да еще и без люфтов), ШД, муфта, крепеж, не забыть шайбу под каждый винт… В общем, намучался. Этот вариант будет печататься из композита (посматриваю на PP GF30). Потом, скорее всего, фрезеровка каретки на этом же станке.
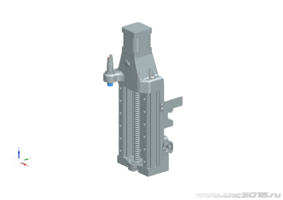
Сама каретка представляет собой П-образную конструкцию, со множеством отверстий и выемок. Ничего сложного. Но есть два проблемных места: 1- ходовой винт оси Z; 2 – ходовая гайка оси X. Пойдем по порядку.
Уберем все лишнее, разрежем и посмотрим на винт ШВП.
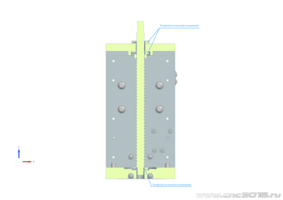
Сверху на винт накручивается гайка низкая М10 (резьбу необходимо нарезать до нужной длины). После этого, винт продевается в два отверстия. Снизу ложится на упорный игольчатый подшипник AXK0821. Сверху через подшипник AXK1024 поджимается гайкой к верхней стенке, тем самым распирается и жестко встает на свое место. После этого накидывается второй подшипник AXK1024 и поджимается второй низкой гайкой М10 (на изображении ее нет, случайно убрал). Гайки садятся на фиксатор резьбы. Так винт без люфтов (очень на это надеюсь) встанет на свое место
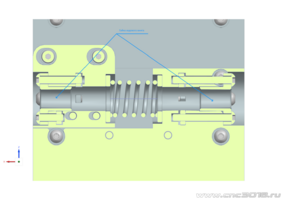
Механизм распорки гаек ходового винта оси X. Обе латунные гайки крепятся через 4 винта М3 к напечатанным деталям. Закручиваться будут в гайки, которые закладываются в деталь на этапе печати (напечатал до нужной высоты, поставил паузу, заложил нужную деталь, продолжил печать), благо что слайсеры позволяют ставить паузы на нужном слое. Левая на картинке гайка подвижная. На каретке фиксируется четырьмя винтами М3 после распорки двух гаек пружиной.
Линейные направляющие MGN12 крепятся к алюминиевому профилю 20х20. Профиль к каретке крепится на пять винтов М3. Пять потому что шестой закрутить не имеется возможности из-за линейного подшипника оси X. С торцов к профилю винтами М6 притянутся верх и низ каретки. Это уменьшит прогиб стенок от распорки ходового винта. Плюс, верхние винты закрепят на каретке кронштейн шагового двигателя оси Z.
Сам кронштейн, помимо своей основной задачи, имеет отросток для установки концевика оси Z и технологическое окно для затягивания винтов на муфте. В целом, по оси X все.
Ось Y (она же стол)
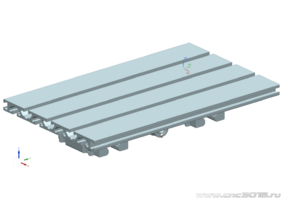
Чего-то интересного тут нет. Решение с распором гайки ходового винта тут точно такое же, как и на оси X. Высота подшипников маловата, относительно того, что было на валах, по тому ставлю небольшую проставку (естественно - печатается). Также есть небольшой кронштейн с металлической пластиной для срабатывания индуктивного датчика.
Ну и напоследок. Рама
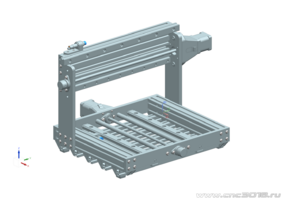
Каких-то серьезных изменений рама не потерпела. Только лишь усилилась и приобрела места под новые рельсы. Рассмотрим подробнее и начнем с основания.
На основание добавилось пять алюминиевых профилей 20х20, которые крепятся через уголки к профилю 40х40. Основной их задачей является удержание линейных направляющих оси Y. Помимо этого, они не плохо так добавили жесткости всей базе станка. Еще одно заметное изменение – это цилиндрические направляющие диаметром 12 мм, которые остались от оригинальной комплектации. Но теперь они играют роль стяжек (или распорок), между передней и задней стенками основания и увеличивают жесткость. Для их установки потребуется просверлить 2 отверстия диаметром 6.5 мм. Для этого будет проектироваться кондуктор. Возможно, имеет смысл добавить кронштейн для каждого профиля 20х20, чтобы дополнительно фиксировать бывшую направляющую, но пока без этого.
Ходовой винт теперь крепится подшипниками KFL08 с обеих сторон и не должен передавать продольную нагрузку на ШД. Для установки дополнительного подшипника в задней стенке рамы необходимо просверлить два отверстия. Кронштейн шагового двигателя оси Y крепится к раме четырьмя винтами М3, которые закручиваются непосредственно в ШД. На нем также имеется технологическое окно. Тут же на раме стоит концевик оси Y. Крутилки на оси решил оставить, может пригодится. Тем более что они есть в наличии. Резиновые ножки встали на свои новые места.
Из-за установки дополнительного подшипника увеличилась необходимая длина ходового винта. Таким образом, винт от оси X немного обрежется и перейдет на ось Y. А на ось X необходимо купить новый винт.
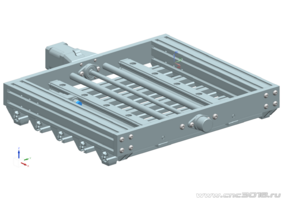
С базой все. Перейдем к порталу
Из крупных изменений тут только профиль 20х60 и линейные направляющие. Так же как и на ось Y, добавлен второй подшипник KFL08, под который требуется просверлить 2 отверстия на правой боковой стойке. Кронштейн ШД оси X крепится через отверстия, которые раньше нужны были для крепления цилиндрических направляющих, через винты М6 с плоской головкой. Это нужно для увеличения рабочего пространства станка. Концевик сидит на профиле 20х60.
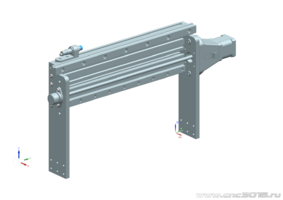
Вроде, обо всем рассказал. Сейчас идет этап печати деталей в пустотелом варианте для проверки их геометрии (на текущий момент уже были выявлены недочеты). Потом станок будет собираться в пустотелом варианте, для проверки кинематики. И только после этого печатать полноценные детали и собирать в полноценный станок. Если можно так выразиться.
Пока что у меня есть надежды, что после доработок станок сможет тягаться с металлами. Хотя бы с цветными. Понятно, что не на заказ на нем работать, а исключительно для себя. Собственно, для этого все и затевалось. Но смущает место крепления портала к базе.
Ну и для удобства обсуждения выкладываю все, что сделал в формате STEP. Надеюсь, мои труды кому-нибудь пригодятся.
Планы на будущее:
1. Заменить все ходовые винты на ШВП. Если будет необходимость, рассмотрю варианты подороже для минимизации люфтов.
1.1. Сделать фрезерованную каретку оси X. Думаю, это входит в планы про ШВП.
1.2. Если фрезерованная каретка осуществится, то постараюсь сделать базовую каретку, а на нее вешай что хочешь. Хочешь – фрезер, хочешь – лазер.
3. Поставить более мощный шпиндель. И пооборотистее. На «Али» видал моторы с 20к оборотами, но очень сомневаюсь в этом. Вопрос пока не изучал.
4. Плата управления. На первое время хватит того, что есть. Но мне нужна четвертая ось.
5. Четвертая ось. Пока не уверен, но что-то мне подсказывает что она закроет часть моих хотелок в плане токарной обработки.
P.S. Заранее огромное спасибо каждому за прочтение всего того, что тут написано и добрый совет. В условиях ограниченного количества свободного времени не хотелось бы чтобы проект затих. Нужно довести его до конца, но есть сомнения в моей компетентности относительно некоторых вопросов. Основная проблема – отсутствие реального опыта фрезерования.
P.P.S. Если проект в целом будет интересен, рассмотрю вариант переделки модели под то, что планировалось изначально. То есть линейные направляющие MGN15.