Чуть больше пол года назад, появилась у меня необходимость сделать станок для лазерной резки больших размеров, при этом затратить как можно меньше средств и максимально воспользоваться тем что есть под рукой.
Станок получился работающим, хотя с большим количеством минусов и необходимости улучшений. Но как есть и вот решил поделиться, для критики и мотивации, так сказать. )
Сразу покажу общий вид как есть сейчас:
Рабочее поле 2,2м на 1,2м. Хотел конечно на 1,5+ м, чтоб лист фанеры стандартный помещался, но уперся в пространство размещения, по этому пока 1,2 с возможностью увеличить.
В качестве основы профтрубы, местами сварка, местами болты. Жестко закреплен к стене анкерами, шатания отсутсвуют.
в качестве ламелей - полосы 40мм, кривущие конечно, но для таких размеров листов в принципе эта кривизна не влияет. В боковых профилях сделаны отверстия, это задел на вытяжку, которую ещё предстоит изобретать совместно с закрытием корпуса, но пока так.
На момент начала постройки конструкционных профилей нужного размера у меня не было и не было плана покупать. Но за то были мебельные профиля от разобранного купе. Их и использовал как опоры для осей.
ровные и в тот момент это было главным.
В них расположены ремни и пот ним катаются на подшипниках каретки.
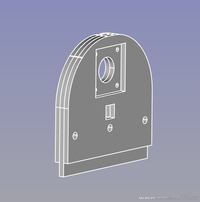
каретки нарисовал во FreeCad из расчета склейки из фанеры 4,5мм Бутербродом в 3 листа.
На одной стороне катается вся электроника. Такое решение принял исходя из того, чтобы минимизировать проводку.
Ось X то же из мебельного профиля, но потоньше, объединена с чем под руку попало. И это да, самая шаткая деталь. Скорости выше 400 на поворотах без колебаний отработать не может. Её однозначно надо менять на конструкционный профиль. Но пока работает и так, быстрее 250-300 скорость не использую.
кабель канал печатный.
Модуль использую 20вт, 450нм
фанеру режу от 3 до 16мм. Компрессор аквариумный 45л/мин
Плата управления - benbox. Улучшать и переделывать буду однозначно.
Ближайшие задачи - это корпус/вытяжка, более жесткий портал и переработка всей оси Х.
Более дальние задачи - откидной стол в переднюю часть для мелочевки и для поворотной оси.
Я хорошо понимаю, что многие скажут что это ужас. Но он стабилен, в таком виде работает уже 7 месяцев и самая большая затрата тут - сам модуль. )
Станок получился работающим, хотя с большим количеством минусов и необходимости улучшений. Но как есть и вот решил поделиться, для критики и мотивации, так сказать. )
Сразу покажу общий вид как есть сейчас:
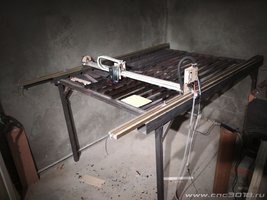
Рабочее поле 2,2м на 1,2м. Хотел конечно на 1,5+ м, чтоб лист фанеры стандартный помещался, но уперся в пространство размещения, по этому пока 1,2 с возможностью увеличить.
В качестве основы профтрубы, местами сварка, местами болты. Жестко закреплен к стене анкерами, шатания отсутсвуют.
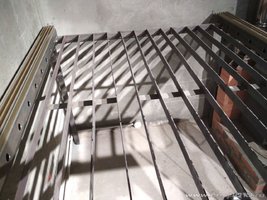
в качестве ламелей - полосы 40мм, кривущие конечно, но для таких размеров листов в принципе эта кривизна не влияет. В боковых профилях сделаны отверстия, это задел на вытяжку, которую ещё предстоит изобретать совместно с закрытием корпуса, но пока так.
На момент начала постройки конструкционных профилей нужного размера у меня не было и не было плана покупать. Но за то были мебельные профиля от разобранного купе. Их и использовал как опоры для осей.
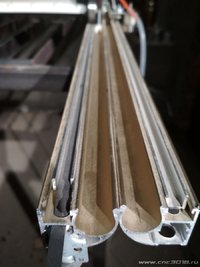
ровные и в тот момент это было главным.
В них расположены ремни и пот ним катаются на подшипниках каретки.
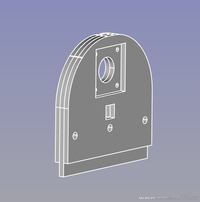
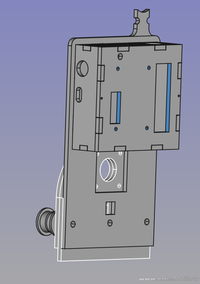
каретки нарисовал во FreeCad из расчета склейки из фанеры 4,5мм Бутербродом в 3 листа.
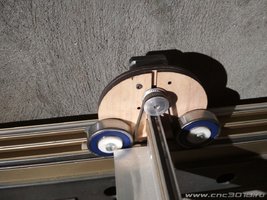
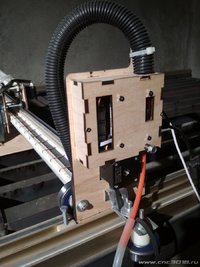
На одной стороне катается вся электроника. Такое решение принял исходя из того, чтобы минимизировать проводку.
Ось X то же из мебельного профиля, но потоньше, объединена с чем под руку попало. И это да, самая шаткая деталь. Скорости выше 400 на поворотах без колебаний отработать не может. Её однозначно надо менять на конструкционный профиль. Но пока работает и так, быстрее 250-300 скорость не использую.
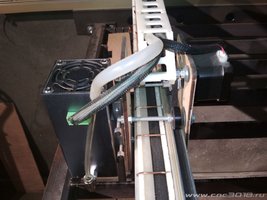
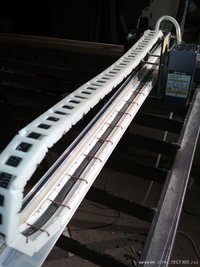
кабель канал печатный.
Модуль использую 20вт, 450нм
фанеру режу от 3 до 16мм. Компрессор аквариумный 45л/мин
Плата управления - benbox. Улучшать и переделывать буду однозначно.
Ближайшие задачи - это корпус/вытяжка, более жесткий портал и переработка всей оси Х.
Более дальние задачи - откидной стол в переднюю часть для мелочевки и для поворотной оси.
Я хорошо понимаю, что многие скажут что это ужас. Но он стабилен, в таком виде работает уже 7 месяцев и самая большая затрата тут - сам модуль. )