Последнее редактирование:
Здравствуйте! Делюсь своими соображениями по поводу одного интересного материала для обработки на нашей китайской малютке. Экструдированный (или экструзионный) пенополистирол (пенопласт). Может я ниже и буду описывать самые банальные и всем известные вещи, но для себя я долго собирал информацию, испытывал на практике и эксперементировал. Так что может быть кому то окажется статья полезной.
Итак, материал идеально подходит для прототипирования, изготовления декора, надписей, мастер моделей для литьевых форм. Неплох в 3D обработке.
Из плюсов:
-Скорость обработки. Для резки и выборки материала использую спиральную однозаходную фрезу 3,175мм. Скорость 10мм/с, но в управляющей программе еще задаю скорость 200%.
-Относительно низкий шум при обработке. При резке и выборке практически не слышно из соседней комнаты с закрытой дверью. При 3D обрабоке пером - слышно только звук шпинделя и шаговых двигателей.
-Относительно прочный. (Ниже приведу пример).
-Дешевый. В Леруа от 75р. за лист 600x1200.
-Быстрая установка на стол.
-Можно особо не переживать за фрезу.
(на фото пример 3D гравировки из скачанного с данного сайта пробного файла. Фреза - перо из комплекта станка, время - 1,5 часа. Пробовал закрасить маркером, иначе на фото крайне плохо видно детали. Размер 5х5 см)
Минусы:
-Опять же прочность. Сами должны понимать - это даже не пластик, какая то серьёзная нагрузка на изделие противопоказана.
-Очень плохо со склейкой. Далеко не каждый клей подойдет, тем более на основе растворителей.
-Термостойкость. Её просто нет. Легко плавится при температуре чуть выше 200 градусов. Боится открытого огня. (может быть использовано как плюс, при изготовлении литьевых форм.
-Химическая стойкость - боится растворителей. Каких точно не перечислю, но большинство часто используемых в быту это точно.
-Самый огромный минус - стружка. Её просто дохрена, она мелкая (не вся, по ссылке на видео ниже можно увидеть как отслаивается стружка при выборке материала). И эта стружка разлетается и налипает просто везде. Все пластиковые поверхности облипнут этой мелкой стружкой полностью.
О последнем пункте хочется поговорить отдельно более подробно. После того, как я начались мои работы с экструдированным пенополистиролом (далее я буду сокращать просто ЭП для краткости), самой большой проблемой стало загрязнение рабочего места и узлов станка. Появилась острая необходимость в отводе стружки от фрезы. Перешерстив этот форум, и некоторые другие, посмотрев в кошелек, поскебшись по сусекам, было решено изготовить систему аспирации самостоятельно. Выбор без раздумий пал на вытяжу в основе которой используется двигатель от жёсткого диска. Благо этого добра у меня имеется. Первый вариант был быстренько собран из того что было под рукой. А под рукой было:
Труба канализационная 110я, заглушка на трубу, угловой элемент трубы 50мм, шланг от сифона, воздуховод из корпуса системного блока, двигатель от жесткого диска (пока что с родным контроллером), вентилятор из корпуса системного блока, мешок из нетканного материала и изолента. Лопасти от вентилятора были насажены на вал двигателя(не каждый вентилятор подойдёт для подобных целей, из трёх, что перепробовал, только лопасти от одного сели как родные, плотненько и нажено даже без клея)
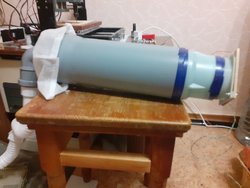
Такая система в принципе показала себя неплохо, но всё же на практике пользоваться ею постоянно было довольно затруднительно. Зато стало понятно в какую сторону нужно копать дальше.
Как стало известно, при уменьшении диаметра входного отверстия, сила всасывания катастрофически падает. Шланг от сифона имел минимальный диаметр 40 мм. Необходимо было больше. Гибкость тоже не радовала. Из того что продавалось не подходило ровным счётом ничего. Наверное было бы отличным вариантом использование гофроканала для укладки кабеля, только где ж его такого большого взять? Было бы неплохо достать вот такой
специально предназначенный для таких целей. Но только где ж его достать чтобы быстро и недорого. И тут меня случайно посетила муза и была придумана следующая схема. Скотч и проволока.
Наматываем скотч с нахлёстом на 50ю трубу, клейкой стороной наружу. Поверх этого наматываем по спирали проволоку. И сверху еще один слой скотча, но уже клеем внутрь. Сказано сделано. Моток проволоки из того же Леруа за 80(? не помню точно) рублей, и моток широкого скотча. Намотал всё на трубу. Использовалась мебельная стойка диаметром 50мм. Результатом был приятно удивлён. Не претендую на идею, возможно такое делали и до меня. Но если кому будет полезной информация от меня, пожалуйста, пользуйтесь
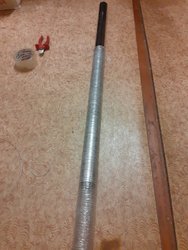
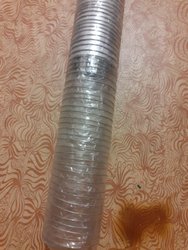
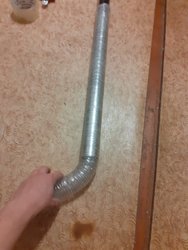
Стало заметно лучше. Шланг держит фонму, достаточно гибкий, и воздух проходит намного лучше чем через шланг от сифона.
Следующим на очереди стал непосредственно вентилятор. И вот тут начинается самое интересное. Как острую необходимость принял то, что вентилятор надо делать центробежный, по типу улитки, посколько по характеристикам всасывания он гораздо эффективнее того, что было у меня в наличии. Первым делом заказал на али контроллер для бесколлекторного двигателя за 200 р. , поскольку родная плата от жёсткого диска после включения останавливала движок через пару минут. Далее закуплен ЭП толщиной 30 мм. ( на деле оказалось что 29). В кореле накиданы чертежи будущего вентилятора. Лопасти и кожух. Все перенесено в аспайр, и создана управляющая программа. На выходе получаем вот такие симпотичненькие детальки.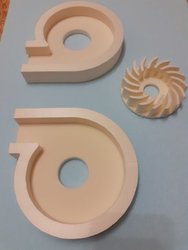
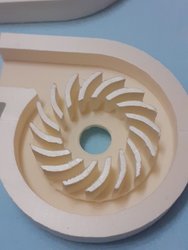
Лопасти рисовал глядя на примеры заводских изделий. Точностью особой не заморачивался, нужно было хотя бы проверить работоспособность идеи. И вот тут мы вспоминаем один из минусов, а именно прочность Толщина кожуха - 1 см. Этого хватает чтобы держать форму и быть довольно прочным. Лопасти-при обработке не одна не пострадала, высота 23мм. От надавливания пальцем сгибается, но не отламывается. Резка крыльчатки по времени заняла минут 40, кожуха - по 20 минут на каждую половину.
Собираем
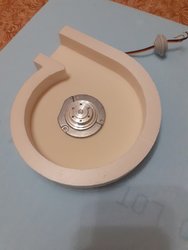
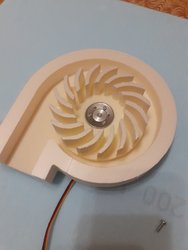
двигатель дополнительно закреплён с внешней стороны деталью из тонкой фанеры.
Дополнительно вырезан переходник для крепления на трубу.
Соединил всё на несколько зубочисток и термоклей. Держится пока неплохо. Щелей нет.
Итог. Результат превзошёл все ожидания. Сила всасывания по сравнению с предыдущим вариантом возросла если не в разы, то заметно больше. По прикидкам, у двигателя скорость вращения приблизительно 10 000 об/мин. Шум есть, но не критичный по сравнению с шумом станка. Вся самая мелкая стружка от фрезы улетает сразу в трубу не разлетаясь по окрестностям. Едиственная проблема на данный момент - как посадить шланг на шпиндель. Пробовал экспериментировать с распаечной коробкой (на одном из фото её видно) но получилось совершенно отвратно и громоздко. Проблему конечно решил бы 3D принтер, но у меня его нет, а заказывать печать в фирме пока не имею возможности. Если у кого есть готовое решение на этот счёт, посоветуйте пожалуйста.
К статье предлагаю небольшую нарезочку видео для наглядности. ссылка на видео
Таймкоды:
0:00-0:05 первый пробный запуск
0:05-0:47 выборка материала, изготовление части кожуха. Видно как в трубу всасываются большие куски стружки. Мелкую стружку на видео не видно, но поверьте мне, её очень много, и сейчас они улетают именно в пылесос.
0:47-1:14 изготовление крыльчатки
1:14-2:53 снова кожух, предпоследний проход. при вырезании детали мостиков не делаю, просто недорезаю до низа 2мм. Потом это всё легко выламывается.
2:53-3:06 первый запуск крыльчатки. Слегка был в шоке от того как сильно дует.
3:06-3:19 запуск в полусобранном состоянии. Можно заметить как конструкцию присосало к руке.
3:19-3:34 запуск в собранном состоянии. Вентилятор присосался к фанере.
3:34-3:55 тест на всасывание 1. Установлена крыльчатка от вентилятора компьютерного. Присасывает кусок ЭП если плотно прижать.
3:55-4:22 тест на всасывание 2. Установлен вырезанный вентилятор. Присасывает Кусок ЭП побольше без проблем даже без прижатия с расстояния несколько миллиметров.
4:22-4:46 собираем стружку. Большие куски застряют
)
И еще пару слов на последок. При вырезке деталей из ЭП по контуру используйте встречное движение фрезы, так поверхность будет гладкой. Пылесоса хватает на одно большое изделие, такое например как часть кожуха, потом нужно вытряхивать стружку. Циклон скорее всего не получится использовать при обработке ЭП, поскольку стружка очень летучая и налипает на всё, что имеет хоть небольшой статический заряд. На шланг кстати не налипает, возможно потому что внутри находится проволока.
Задавайте вопросы, буду рад ответить. Возможно какие то моменты упустил. Так же буду рад советам и критике. И еще больше буду рад, если статья окажется полезной для Вас.
Еще несколько фотографий.
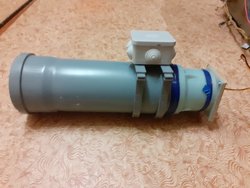

итоговый результат
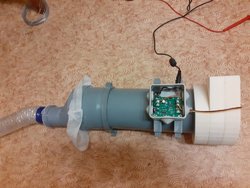
Итак, материал идеально подходит для прототипирования, изготовления декора, надписей, мастер моделей для литьевых форм. Неплох в 3D обработке.
Из плюсов:
-Скорость обработки. Для резки и выборки материала использую спиральную однозаходную фрезу 3,175мм. Скорость 10мм/с, но в управляющей программе еще задаю скорость 200%.
-Относительно низкий шум при обработке. При резке и выборке практически не слышно из соседней комнаты с закрытой дверью. При 3D обрабоке пером - слышно только звук шпинделя и шаговых двигателей.
-Относительно прочный. (Ниже приведу пример).
-Дешевый. В Леруа от 75р. за лист 600x1200.
-Быстрая установка на стол.
-Можно особо не переживать за фрезу.
(на фото пример 3D гравировки из скачанного с данного сайта пробного файла. Фреза - перо из комплекта станка, время - 1,5 часа. Пробовал закрасить маркером, иначе на фото крайне плохо видно детали. Размер 5х5 см)
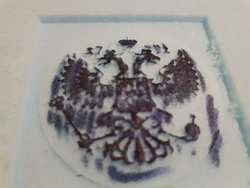
Минусы:
-Опять же прочность. Сами должны понимать - это даже не пластик, какая то серьёзная нагрузка на изделие противопоказана.
-Очень плохо со склейкой. Далеко не каждый клей подойдет, тем более на основе растворителей.
-Термостойкость. Её просто нет. Легко плавится при температуре чуть выше 200 градусов. Боится открытого огня. (может быть использовано как плюс, при изготовлении литьевых форм.
-Химическая стойкость - боится растворителей. Каких точно не перечислю, но большинство часто используемых в быту это точно.
-Самый огромный минус - стружка. Её просто дохрена, она мелкая (не вся, по ссылке на видео ниже можно увидеть как отслаивается стружка при выборке материала). И эта стружка разлетается и налипает просто везде. Все пластиковые поверхности облипнут этой мелкой стружкой полностью.
О последнем пункте хочется поговорить отдельно более подробно. После того, как я начались мои работы с экструдированным пенополистиролом (далее я буду сокращать просто ЭП для краткости), самой большой проблемой стало загрязнение рабочего места и узлов станка. Появилась острая необходимость в отводе стружки от фрезы. Перешерстив этот форум, и некоторые другие, посмотрев в кошелек, поскебшись по сусекам, было решено изготовить систему аспирации самостоятельно. Выбор без раздумий пал на вытяжу в основе которой используется двигатель от жёсткого диска. Благо этого добра у меня имеется. Первый вариант был быстренько собран из того что было под рукой. А под рукой было:
Труба канализационная 110я, заглушка на трубу, угловой элемент трубы 50мм, шланг от сифона, воздуховод из корпуса системного блока, двигатель от жесткого диска (пока что с родным контроллером), вентилятор из корпуса системного блока, мешок из нетканного материала и изолента. Лопасти от вентилятора были насажены на вал двигателя(не каждый вентилятор подойдёт для подобных целей, из трёх, что перепробовал, только лопасти от одного сели как родные, плотненько и нажено даже без клея)
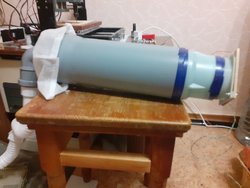
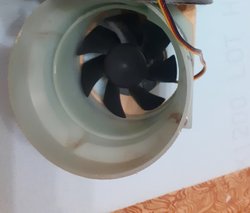
Такая система в принципе показала себя неплохо, но всё же на практике пользоваться ею постоянно было довольно затруднительно. Зато стало понятно в какую сторону нужно копать дальше.
Как стало известно, при уменьшении диаметра входного отверстия, сила всасывания катастрофически падает. Шланг от сифона имел минимальный диаметр 40 мм. Необходимо было больше. Гибкость тоже не радовала. Из того что продавалось не подходило ровным счётом ничего. Наверное было бы отличным вариантом использование гофроканала для укладки кабеля, только где ж его такого большого взять? Было бы неплохо достать вот такой
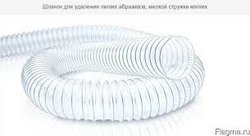
специально предназначенный для таких целей. Но только где ж его достать чтобы быстро и недорого. И тут меня случайно посетила муза и была придумана следующая схема. Скотч и проволока.
Наматываем скотч с нахлёстом на 50ю трубу, клейкой стороной наружу. Поверх этого наматываем по спирали проволоку. И сверху еще один слой скотча, но уже клеем внутрь. Сказано сделано. Моток проволоки из того же Леруа за 80(? не помню точно) рублей, и моток широкого скотча. Намотал всё на трубу. Использовалась мебельная стойка диаметром 50мм. Результатом был приятно удивлён. Не претендую на идею, возможно такое делали и до меня. Но если кому будет полезной информация от меня, пожалуйста, пользуйтесь
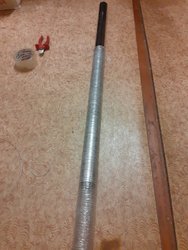
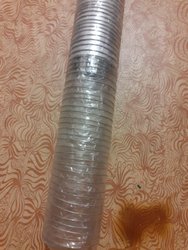
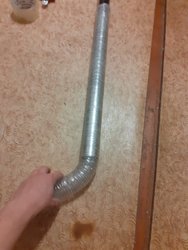
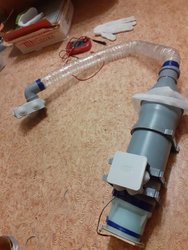
Стало заметно лучше. Шланг держит фонму, достаточно гибкий, и воздух проходит намного лучше чем через шланг от сифона.
Следующим на очереди стал непосредственно вентилятор. И вот тут начинается самое интересное. Как острую необходимость принял то, что вентилятор надо делать центробежный, по типу улитки, посколько по характеристикам всасывания он гораздо эффективнее того, что было у меня в наличии. Первым делом заказал на али контроллер для бесколлекторного двигателя за 200 р. , поскольку родная плата от жёсткого диска после включения останавливала движок через пару минут. Далее закуплен ЭП толщиной 30 мм. ( на деле оказалось что 29). В кореле накиданы чертежи будущего вентилятора. Лопасти и кожух. Все перенесено в аспайр, и создана управляющая программа. На выходе получаем вот такие симпотичненькие детальки.
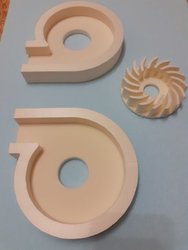
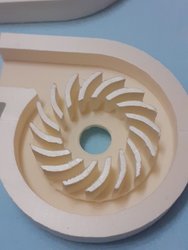
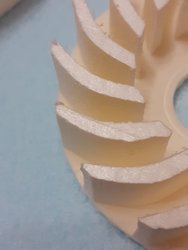
Лопасти рисовал глядя на примеры заводских изделий. Точностью особой не заморачивался, нужно было хотя бы проверить работоспособность идеи. И вот тут мы вспоминаем один из минусов, а именно прочность Толщина кожуха - 1 см. Этого хватает чтобы держать форму и быть довольно прочным. Лопасти-при обработке не одна не пострадала, высота 23мм. От надавливания пальцем сгибается, но не отламывается. Резка крыльчатки по времени заняла минут 40, кожуха - по 20 минут на каждую половину.
Собираем
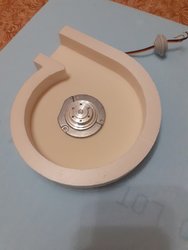
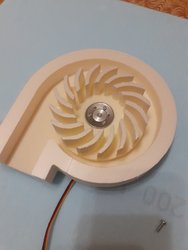
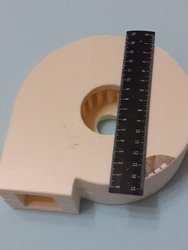
двигатель дополнительно закреплён с внешней стороны деталью из тонкой фанеры.
Дополнительно вырезан переходник для крепления на трубу.

Соединил всё на несколько зубочисток и термоклей. Держится пока неплохо. Щелей нет.
Итог. Результат превзошёл все ожидания. Сила всасывания по сравнению с предыдущим вариантом возросла если не в разы, то заметно больше. По прикидкам, у двигателя скорость вращения приблизительно 10 000 об/мин. Шум есть, но не критичный по сравнению с шумом станка. Вся самая мелкая стружка от фрезы улетает сразу в трубу не разлетаясь по окрестностям. Едиственная проблема на данный момент - как посадить шланг на шпиндель. Пробовал экспериментировать с распаечной коробкой (на одном из фото её видно) но получилось совершенно отвратно и громоздко. Проблему конечно решил бы 3D принтер, но у меня его нет, а заказывать печать в фирме пока не имею возможности. Если у кого есть готовое решение на этот счёт, посоветуйте пожалуйста.
К статье предлагаю небольшую нарезочку видео для наглядности. ссылка на видео
Таймкоды:
0:00-0:05 первый пробный запуск
0:05-0:47 выборка материала, изготовление части кожуха. Видно как в трубу всасываются большие куски стружки. Мелкую стружку на видео не видно, но поверьте мне, её очень много, и сейчас они улетают именно в пылесос.
0:47-1:14 изготовление крыльчатки
1:14-2:53 снова кожух, предпоследний проход. при вырезании детали мостиков не делаю, просто недорезаю до низа 2мм. Потом это всё легко выламывается.
2:53-3:06 первый запуск крыльчатки. Слегка был в шоке от того как сильно дует.
3:06-3:19 запуск в полусобранном состоянии. Можно заметить как конструкцию присосало к руке.
3:19-3:34 запуск в собранном состоянии. Вентилятор присосался к фанере.
3:34-3:55 тест на всасывание 1. Установлена крыльчатка от вентилятора компьютерного. Присасывает кусок ЭП если плотно прижать.
3:55-4:22 тест на всасывание 2. Установлен вырезанный вентилятор. Присасывает Кусок ЭП побольше без проблем даже без прижатия с расстояния несколько миллиметров.
4:22-4:46 собираем стружку. Большие куски застряют
И еще пару слов на последок. При вырезке деталей из ЭП по контуру используйте встречное движение фрезы, так поверхность будет гладкой. Пылесоса хватает на одно большое изделие, такое например как часть кожуха, потом нужно вытряхивать стружку. Циклон скорее всего не получится использовать при обработке ЭП, поскольку стружка очень летучая и налипает на всё, что имеет хоть небольшой статический заряд. На шланг кстати не налипает, возможно потому что внутри находится проволока.
Задавайте вопросы, буду рад ответить. Возможно какие то моменты упустил. Так же буду рад советам и критике. И еще больше буду рад, если статья окажется полезной для Вас.
Ваши сообщения автоматически объединены:
Еще несколько фотографий.
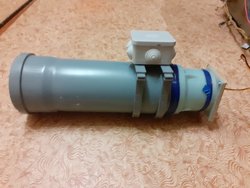

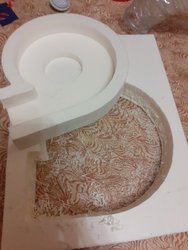
итоговый результат
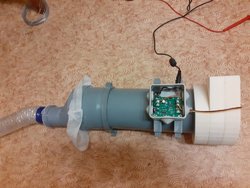